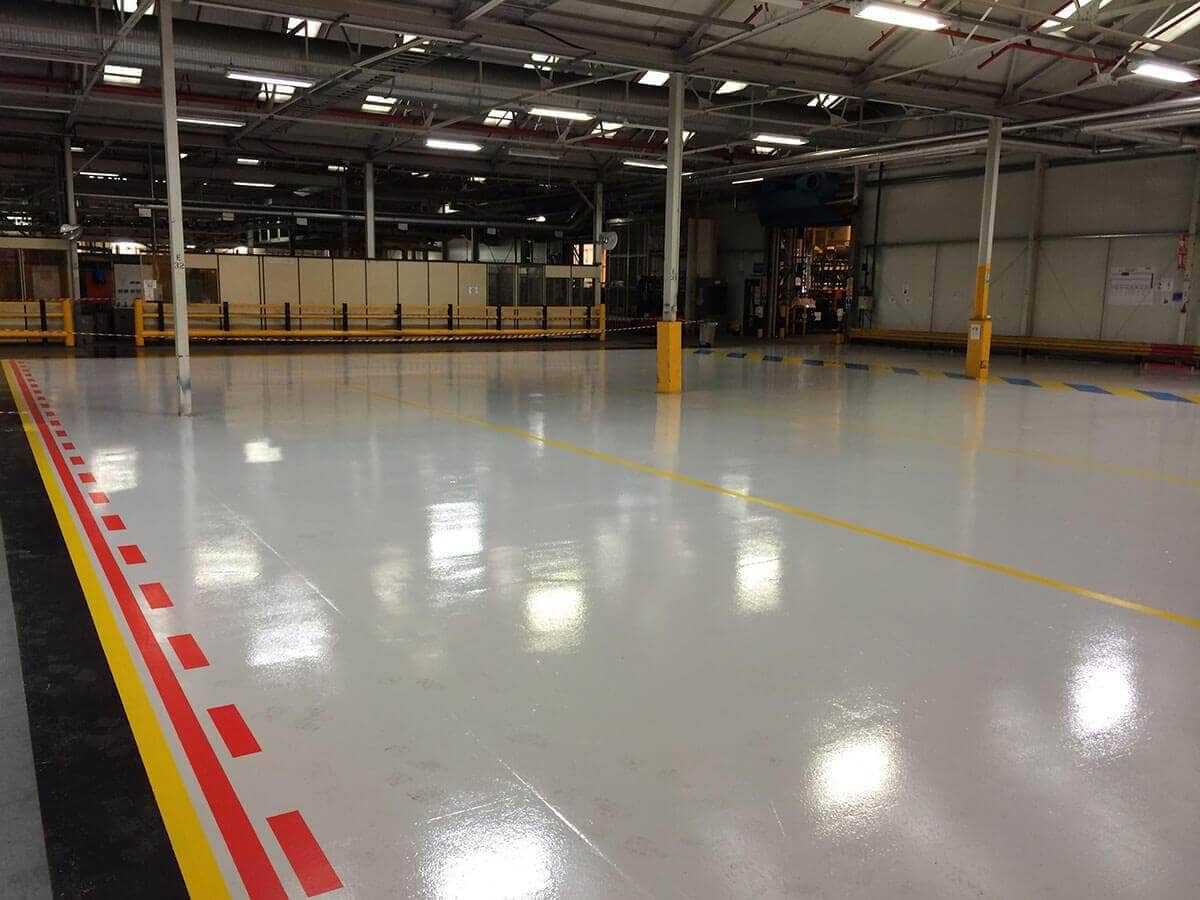
The UK’s leading resin flooring specialist
Troubleshooting Guide to Epoxy Flooring Problems
Epoxy flooring is a popular and cost-effective choice for businesses and other commercial properties. However, as with any flooring option, potential problems can occur during installation or use. This troubleshooting guide will help business owners and property managers identify and fix the root causes of epoxy floor problems.
Peeling
If the epoxy appears to be peeling following installation, it could be due to several factors:
No primer used
Before installing the epoxy, all base surfaces must be appropriately prepared and primed. The right kind of primer can help improve durability, especially when working with a porous base material such as concrete which needs to be ‘sealed’ to improve adhesion.
Humid conditions
Epoxy flooring can be susceptible to damage in humid conditions. Therefore, if the property is particularly damp or humid, it is essential to take measures to protect the epoxy from moisture.
Preventative measures can include installing a moisture barrier or using a dehumidifier in the area.
Contaminants on the base layer
Grease and oil can be a common problem for epoxy flooring. If these contaminants are not removed properly from the base substrate, they can cause the epoxy to peel or chip.
It is important to use a degreaser and a scrub brush to remove grease and oil. Be sure to rinse the area thoroughly afterwards to remove any residual cleaner.
Improper surface preparation
It is essential to prepare the surface correctly before installation, including cleaning the area thoroughly and making necessary repairs. In addition, grinding or sanding the concrete will improve the adhesion between the underlayer and the epoxy.
Poor substrate quality
If the surface is damaged, or if the underlying material is not strong enough, the epoxy can start to peel. Therefore, it is important to ensure that the underlying material is sturdy and in good condition.
In addition, it may be necessary to apply further coats of primer to improve the strength of the base. A weak substrate is not suitable for an epoxy resin floor.
Wrong proportions
If you use the wrong ratios of epoxy and hardener, or if the mix is not blended correctly, the epoxy won’t cure properly and could start to peel. Be sure to mix the epoxy and hardener thoroughly and use the correct proportions.
Trapped particles
To prevent dust and dirt particles from getting trapped in your flooring, thoroughly clean it before applying the epoxy. Use a soft brush to remove larger pieces of dirt and debris, and follow this with an industrial hoover to remove fine particles that may still be present on the surface.
Lastly, close all windows before the epoxy installation to avoid disturbing and circulating dust and other contaminants while the epoxy is still curing.
Epoxy isn’t smooth
Epoxy isn’t smooth
Another possible problem is that the finished epoxy can look rough or bumpy. A number of things can cause this, such as:
Too little product used
If you don’t use enough epoxy, it can lead to an unequal finish. The product will not be able to cover the surface evenly or self-level, and some areas will be thicker than others. As a result, these areas may become rough or uneven.
Too much product used
Conversely, it is also possible to apply too much epoxy, which will also affect the quality of the finish. When the epoxy is too thick, it will not cure uniformly and can leave a bumpy or textured surface.
Incomplete mixing
When the mixture components are not combined properly, the epoxy will not set at the same rate and can cause the flooring to have an irregular finish.
Inadequate tools
Old and worn tools may not be able to apply the epoxy evenly or smoothly, which will show in the final product.
Low Temperatures
When the environment is too cold, the epoxy may not set correctly, affecting the smoothness of the finish. When applying the epoxy flooring, ensure the ambient temperature is warm enough and avoid working in extreme temperatures.
When the product does not flow properly due to low temperatures, it might be necessary to add some solvent.
Obvious roller marks
Pinholes and air bubbles can be a nuisance when applying epoxy flooring. Various factors can cause this, including:
Insufficient mixing
The epoxy resin and hardener must be thoroughly combined to reduce the formation of air bubbles. For example, keeping the mixer’s paddle too close to the surface or pumping the paddle up and down can drag air into the mixture and cause bubbles to form.
Not enough primer
Concrete is a porous material, which means that it can easily absorb liquids. Air bubbles can become trapped between the base and epoxy layers if you don’t adequately prime the surface. The air bubbles will rise as the epoxy cures, resulting in visible pinholes.
Moisture under the epoxy
If moisture is present in the concrete substrate, it can cause the epoxy to bubble. This complication is often due to droplets of liquid in the pores of the concrete and can be a particular problem if the concrete is newly laid and not fully dry.
As a result, if the surface is not sealed correctly before applying the epoxy, moisture can become trapped and cause the adhesive bond to diminish and lead to air bubbles.
Extreme ambient conditions
The temperature and humidity of the surrounding area can also cause bubbles to form in the epoxy. If it is too hot or humid, the epoxy will cure too quickly and not have time to properly self-level. This situation can cause the epoxy to trap air bubbles inside, which will rise to the surface as it cures.
Too cold, and the epoxy will not flow well enough to level out, resulting in air bubbles. Maintaining consistent environmental conditions during installation and the curing process is vital to stop this problem.
Incorrect application
Even if you’re using the correct products and following all the proper procedures, bubbles can still form if you do not install the epoxy with care. If it’s not spread evenly or you apply too much at once, it can cause air pockets to get trapped. Use a roller to apply the epoxy in thin coats and avoid flooding the surface.
Not curing properly
Many factors affect the curing process of epoxy resin floors. Some of the most common are:
Too little hardener
When there is too little hardener in the resin, it will not cure properly. It can result in the floor being soft and spongy or even sticky and lead to other problems, such as delamination and cracking.
Improper mixing
When the epoxy and hardener are not combined thoroughly, it can lead to inadequate chemical bonding and poor curing. Using an electric mixer ensures a more thorough blending of the materials.
Ambient temperature
If the ambient temperature is too cold or too hot, it can slow down or stop the curing process. The ideal temperature range for curing epoxy resin is 24-29 degrees Celsius.
Bumps in the epoxy
When the epoxy is curing, tiny bumps or lumps will sometimes form on the surface due to:
Air bubbles
If the mixture contains too much air, it can cause the epoxy to form bubbles on the surface. These bubbles will eventually burst and leave behind bumps or ridges.
Pre-existing defects
When the base substrate is not well cleaned and prepared before epoxy application, it can cause bumps and irregularities in the finished flooring.
Inferior application
Improperly applying the epoxy resin can also lead to bumps or ridges on the surface. It is often caused by not spreading the material evenly or using too much or too little product.
Flooring appears dull
When the room humidity is too high, epoxy can suffer from a flooring defect known as amine blush. It causes the epoxy flooring to look dull and cloudy. The leading cause of amine blush is moisture, which can be from the surrounding air, the epoxy material itself or the substrate to which it is applied.
If there is too much moisture present, it can cause the epoxy to re-emulsify, leading to a bluish-white film on the surface. Therefore, the ideal temperature range needs to be at least 3-4 degrees Celsius above the dew point to prevent this.
Patchy finish with colour disparities
Moisture on the curing epoxy can cause a patchy finish with colour disparities. It happens because the wet areas do not cure at the same rate and will have a different appearance than the rest of the surface.
To prevent this, check for leaky air conditioning ducts or dripping overhead piping, allowing time to address any issues and the area to dry completely before starting the epoxy application.
Conclusion
Epoxy flooring is a great way to protect and enhance your commercial space, but like any other surface treatment, it’s not immune to issues. By following the advice in this troubleshooting guide, you should be able to identify and fix the most common causes of epoxy flooring problems before installation.
Contact Us
At Impact Floors, we’re experts at installing and maintaining resin flooring. If you have any further questions, need assistance with troubleshooting epoxy flooring problems, or would like advice on the best resin flooring for your business, please don’t hesitate to contact us. Our team will be happy to help!